Precise cuts and ultrasonic welding with a digital control of the parameters
Easy to use, easy to programme with unmatched precision of welding. DIGITAL Thorn+ welder and its wide spectre of possibilities is on a par with top class welders ( SUPER Thorn), produced using the same technology, perfectly suited for the most challenging applications.It guarantees maximum repetitiveness of the welding process, high reliability, and shorter working cycle. Designed for tasks, where output parameters control is essential and the ability to generate charts is not as important.
Standard frequencies are 20, 30, 35 and 40kHz.
Proven, reliable control panel Thorn+
Designed for fast, easy and transparent communication interface between the machine and the operator. Thanks to it, all parameters or welding effects control becomes pure pleasure.Constant parameters control within independently defined rules, leads to higher quality of the welding process.
In a case when certain different elements are being welded , we can define up to 128 different memory entries , which can be chosen externally. The possibility to set initial downthrust pressure and the pressure while welding enables obtaining the best possible connection ( 4 pressures available) . Additionally we are able to control such ad-ons as rotary table , soundproof cabin, adjustable table, tape drive etc. And the history of welds performed ( both correct and incorrect ones) we are able to export via RS-232/485 protocol.
Available welding options:
- Time: welding using constant time
- Energy: welding using constant energy
- Power: welding using constant power
- Total depth (ABS): welding to a given depth
- Relative depth (DRM): welding to a given depth
Digital control panel, SONICTECH’s precision
Every Thorn+ DIGITAL series machine has been equipped with pressure control technology using proportional valves. Using that we are able to set, with digital precision, each of the pressures required (every 0,1 bar)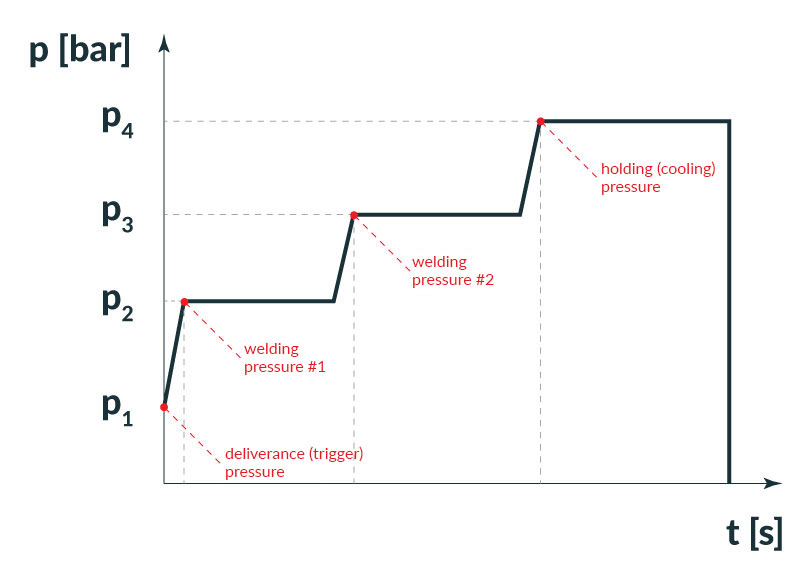
P2 – welding pressure 1
P3– welding pressure 2
P4 – holding ( cooling ) pressure
The welding path is controlled with a precision up to 10μm, thanks to the implementation of position encoder.
All of the above wouldn’t be possible if we weren’t able to sustain welders stiffness, which we obtained by using special combination of iron and aluminium (35kHz)